This article discusses a theoretical 10 Steps that can be taken when striving to complete the elusive Perfect Stocktake. Conducting a Stocktake can be a daunting task. It's a time-consuming necessity, sometimes a dreaded task, and can be very difficult to perfect. Whether you're a rookie to the industry or a veteran Operations Manager, periodical Stocktakes can make or break your Organisation's or Venue's P L. A seemingly innocuous clerical error can have a drastic effect on reporting.
This article discusses a theoretical 10 Steps that can be taken when striving to complete the elusive Perfect Stocktake.
Conducting a Stocktake can be a daunting task. It's a time-consuming necessity, sometimes a dreaded task, and can be very difficult to perfect. Whether you're a rookie to the industry or a veteran Operations Manager, periodical Stocktakes can make or break your Organisation's or Venue's P&L. A seemingly innocuous clerical error can have a drastic effect on reporting. An unposted receipt or transfer can inflate stock on hand for one period and then skew it negatively in the next.
Fear not - the perfect Stocktake is attainable; it starts with proper preparation; add in diligent Product Maintenance, adhering to proper Stock Control methods throughout the Period, and set your Counting process up for success - and Bepoz can help with the entire process.
1. Accurate Product Sizes
Before any stock is counted, it's essential that all Product Purchase and Selling Sizes are accurate and correct in BackOffice. When a new Product is first added into BackOffice, the Base Size, Purchase Size and selling Size/s need to be accurately entered for each Product.
For example, if a vodka is added to your Product List, the Base Unit will most likely be 1 Bottle; this means that the Base Size will need to be the volume of each bottle. Accuracy here is essential - is it a 750-milliliter bottle or a full liter? If you purchase both Sizes, add a Product into your System for each; this will making counting Stock MUCH easier. Next, how are these Bottles being purchased? 6 per case? 12 per case? Lastly, how will the vodka be sold? Give each Size a Name that makes sense, and enter the quantities relevant to the Base Size. Keep in mind, that the selling Size/s can change for each Store that the Product is sold in. Maybe one of your bars sells the full bottle for table service, while others only sell a single or double pour.
2. Accurate Product Costs
As Product is Received from Suppliers, Costs should be updated accurately each time. That case of 12 bottles of vodka may have been $420 the last time you Purchased it, but if your Supplier jacks the Price up to $550, that's a 31% increase and more than a $10 increase per Bottle. If that Cost isn't updated straight away, it will eventually catch up and negatively impact your post-Stocktake reporting. If a Price increase isn't updated prior to a Stocktake, your System will think the Product was purchased at the wrong Price; your costs will beg to differ. Your invoices and your reporting will not add up and it might not be caught until it's too late. Especially if it's a Product that really moves in your Venue.
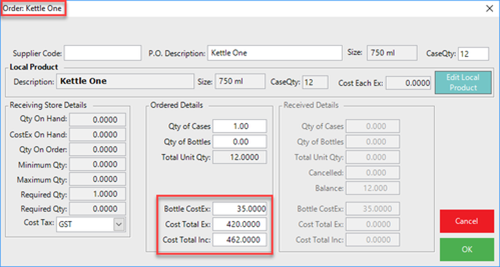
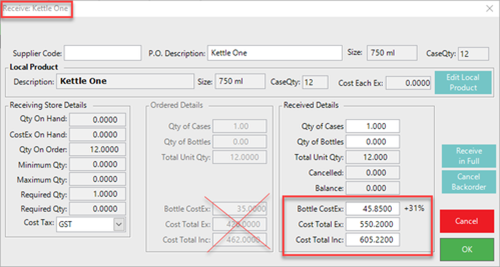
3. Adjust & Post Purchase Orders
As Product is Received, Purchase Orders should be updated and Posted accordingly. This means that each Product on that P.O. must be checked off against what was ordered and adjustments need to be made. It cannot be overstated how crucial this step is to Stock Control or how important accuracy in Receiving P.O.s is to obtaining a perfect Stocktake. This step can be time-consuming when receiving a large order, but an oversight here will carry over into post-Stocktake reporting. If you're expecting to receive 5 cases of vodka, but your supplier shorts you half a case - aside from the potential of running into a Stock shortage for a busy weekend - this must be caught and corrected before the P.O. is marked as Received and the Receipt is Posted. And then, have a nice chat with your supplier rep.
After Product receipt and adjusting any received cases or units - don't forget to Post each P.O. Receipt, even if Product/s is only Partially Received. An Unposted Receipt makes it look like your Stock on Hand grew overnight by itself. That can't be good for Stock Controls or reporting, can it?
If it's decided to leave that Product short and you'll reorder the necessary quantity on your next order, Cancel the Backorder for the P.O. and Post the Receipt.
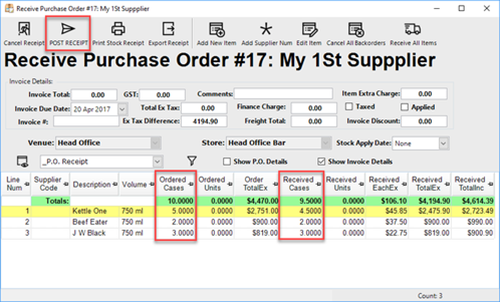
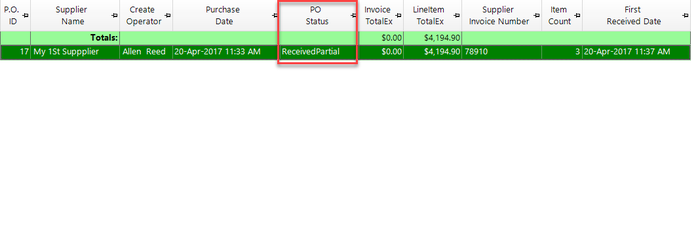
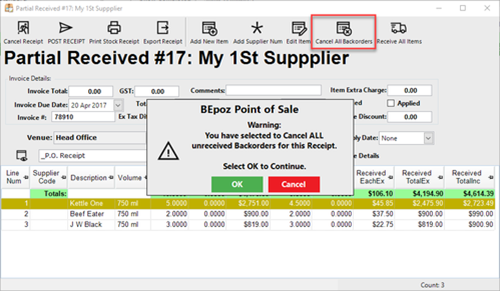
4. Track all Stock Transfers
Any Transfers between Stores need to be tracked and entered as Stock Transfers when the Product moves from one location to another. Even if the Stock was received correctly and accurately, any untracked Transfers will skew numbers for the individual locations involved. If your main bar Transfers a few bottles back to your Warehouse or to another bar but the Transfer isn't tracked - where'd those bottles go?? Did Johnny Bartender sneak them out in his bag?
Your overall Stock on Hand hasn't changed, so does it really matter? In short, YES. If Transfers are consistently tracked, it's easier to spot potential theft when Product really does go missing. Also, your Stocktake for each Store will be so much closer to being perfect.
5. Update Stock Adjustments & Wastage
Sometimes, things don't go perfectly - your Supplier can make a mistake that isn't caught causing a Receipt to be Posted incorrectly; a Stock Transfer doesn't get Tracked and a bar ends up with an extra case of wine
?; a half-full bottle falls off the back bar and shatters.
Whatever the case may be, Adjust that Stock! Adjustments or Re-Initialisations can be entered easily in BackOffice and Wastage (Stock Loss) can be Tracked from a SmartPOS Workstation right then and there.
6. Decide - Full or Partial Stocktake?
Before starting a Stocktake, you'll need to consider whether it will be a Full or Partial Stocktake.
In a Full Stocktake, any Product that is not counted will have its Quantity on Hand set to zero when the Stocktake is applied.
In a Partial Stocktake, only Products that have been counted will be updated; all other Products will retain their theoretical QOH as the QOH after the Stocktake is applied. This will include any actual counts of zero.
Both methods have advantages depending on your preferences and needs. Maybe you'd like to perform a Partial Stocktake weekly on certain Products, but a Full Stocktake monthly? Maybe you'd like to reset your QOH for all packaging to zero rather than counting them?
Also, you can select which Stores in each Venue you'd like to do a Stocktake for - decide if you want a particular Stocktake to be for your entire Venue or for select Stores.
Pro-tip: If a Stocktake isn't initiated in BackOffice, any Stocktake started from a SmartPOS Workstation will default to Partial.
7. Print Count Sheets that Make Sense
Printing Count Sheets for Manual Stocktake may not seem that important, but if done correctly, it can make counting much easier and can reduce the chance of making a counting error.
For starters, decide if you'd like to print your Count Sheets with theoretical QOH or not; from the Stocktake Entry tab, change the View to _CountSheetQty. Alternatively, select _CountSheet to omit theoretical QOH.
Secondly, select and Print out Count Sheets by Product Groups that will make sense when it comes to actually counting. This will be different for each Organisation, however, something to keep in mind is that it may be easier to have fewer Products on a count sheet rather than having an entire Store's Product List together. For instance, break your Count Sheets down based on how Products may be organized in the location. Or, in the same sense, order your Count Sheet list by Parent Group Name as that will more than likely carry over into how Products are organized in reality in your location. If your packaged beer & cider is kept in a refrigerator separate from other cold Products, Print a separate Count Sheet for that Product Group.
Thirdly, if you know that you have multiple Base Sizes of the same Product, you should have separate Product Lines for each.
8. Precise Counting and Count Entry
Counting and Count Entry - so important. A decimal point in the wrong place or an extra zero where it doesn't belong could equate to a veritable disaster. Maybe 'disaster' seems a bit drastic, but don't tell that to a Purchasing Manager that doesn't remember ordering 390 kegs of Guinness last month. Common sense goes a long way here.
If the person Entering Counts isn't the person physically Counting, everyone needs to be on the same page. If a Product isn't counted by the Each, typically, tenths of a whole are the best way to Count. For instance - 1.8 Jars of Olives; fractions can get messy.
Even if the most precise Counting has been conducted, attention to detail when those Counts are being Entered is critical to having a perfect Stocktake. Not sure if Johnny Bartender counted '11' bottles of Merlot or '17'? Double-check before Entering the Count. Also, if a Product on the list wasn't Counted, it may be wise to investigate sooner rather than later.
9. Check Variances, Recount & Re-Enter
Spotting Product Variances prior to Applying a Stocktake is not only of vital importance, but it's also easy. From the Count Entry in BackOffice, Qty Difference, CostEx Difference, and Variance% are the best places to look.
Any large Variances should be investigated. The Product should be Recounted and Re-entered if a new Counted Quantity is found.
A lot of smaller variances can add up quickly, so even if a Product Variance % is off by single digits, it could be worth Recounting, in the long run, to ensure accuracy prior to Applying the Stocktake.
Pro Tip: Sort your Product List by either Qty Difference or Variance% to spot the larger Variances easier.
Don't forget to use the Un-Entered Only flag to slim down your Product List to view Products that haven't had a Counted Quantity Entered yet.
As a fail-safe, before Applying a Stocktake, the overall Variance % for the Venue and for each Store will be displayed. If it's too high for your liking (or per your Organisation's standards) - investigate!
10. Apply the Stocktake
It should go without saying, but it needs to be said - DON'T FORGET TO APPLY YOUR STOCKTAKE. After all of the hard work you've just put in, what good is an Unapplied Stocktake?
If you've been keeping up so far, your Stock Control methods are the envy of the industry and your meticulous Counting and Entry can't fall by the wayside now!
G'head and click that APPLY STOCKTAKE button if you're satisfied with your Counts. The QOH in your system will be updated and you'll have come full circle back to the start of your next Perfect Stocktake.